How a Great 3PL Partner Can Help You Avoid Mayhem During a Product Recall
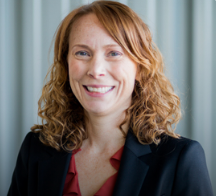
Alex Ohlinger
Head of Marketing
Have you experienced a product recall? It can be a nightmare for any business. One such problem could lead to a substantial profit loss, hefty lawsuits, and a bad reputation.
So what’s the solution? A great 3PL partner who can help you avoid the mayhem and ensure a seamless recall process. The importance of selecting the right third-party logistics partner cannot be overstated. They can bring in their industry experience, expertise, and global logistics to ensure that recalls are executed smoothly and quickly.
In turn, this helps you minimize the damage to your brand’s reputation and the loss of profits. This article highlights the benefits of forming partnerships with 3PL partners for businesses, including those in e-commerce fulfillment (not drop shipping). Trust us, having a great 3PL partner can make all the difference during a product recall.
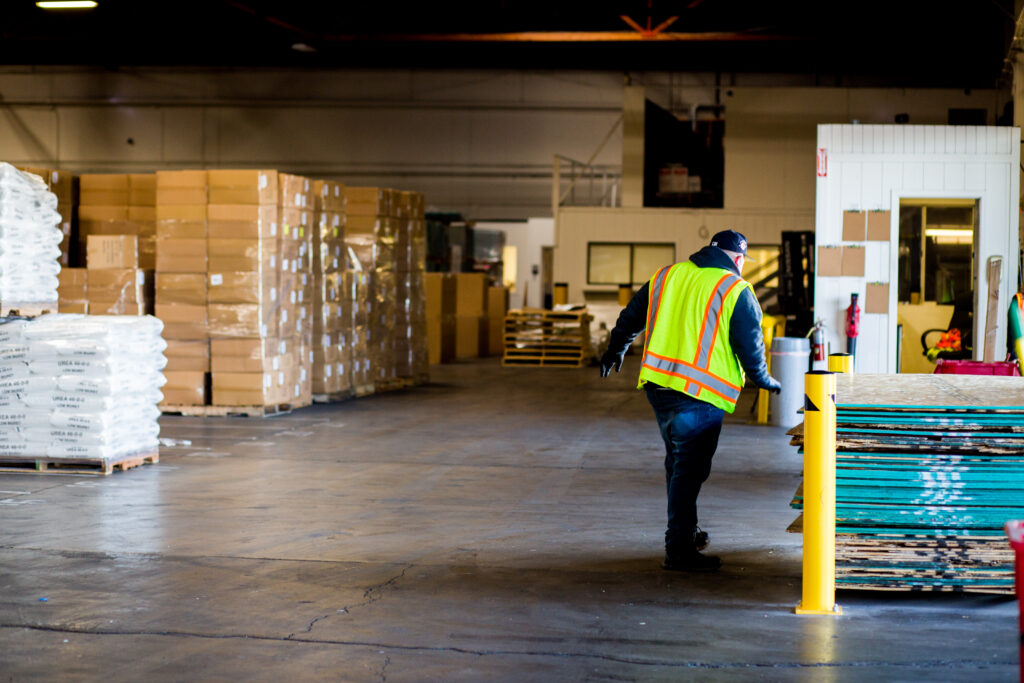
Understanding Product Recalls
“A product recall is an event in which a company attempts to collect defective products moving downstream in the supply chain or have reached the final customer. Often times the product can be harmful to the end user, hence the speed and management of the recall are critical to its success.”- Emily Carow
Product recalls can be costly and detrimental to businesses, so proactive management is necessary to prevent such risks. A recall is issued to protect consumers and the company’s reputation when a product defect is discovered. However, the recall process can be manageable for businesses with a solid plan and experienced partners, such as a third-party logistics (3PL) partner.
Defining Product Recalls
Product recalls occur when a company identifies a defect in its development that poses a significant hazard to the consumer’s health and safety. The product must be removed from the market and, in some cases, from the customers who have already purchased the product. Companies are responsible for providing a remedy to affected customers- including repairs, replacements, or refunds.
Consequences of Product Recalls
Product recalls can impact a business in several ways- financial, reputational, and legal consequences. Failing to manage a recall effectively can result in significant financial losses and loss of customer trust and reputation.
Additionally, companies may face legal repercussions if they mishandle a recall- including lawsuits or regulatory fines. Therefore, it is crucial to have a plan to mitigate these risks and quickly address the issue.
The Complexities of Recall Management
Recall management can be incredibly complex- requiring careful coordination and extensive knowledge of the supply chain, inventory management, and logistics. Businesses must identify the affected products, notify impacted customers, and manage the transportation of the recalled products. This process is further complicated if the company’s products require specialized storage and transport services, such as in cold or temperature-controlled environments.
These challenges are why many companies choose to partner with a third-party logistics provider experienced in handling global logistics to help manage the recall process effectively. By partnering with a 3PL provider, businesses can benefit from the provider’s expertise and resources in managing product recalls. The 3PL partner can help monitor inventory and locate the affected products quickly, streamline communication with customers, and manage the logistics of transporting the recalled products. Therefore, it is essential to have a solid partnership with a 3PL provider to ensure that the recall process is conducted professionally, promptly, and efficiently.
The Role of a Great 3PL Partner
A product recall is, without a doubt, an arduous process that could severely affect any business’s reputation, finances, and public perception. This is why partnering with a reliable third-party logistics (3PL) provider is an excellent strategy to mitigate the risks and pressures of a recall scenario.
They bring expertise and resources to help businesses navigate the recall with minimal disruption to their operations, ensuring the process runs as smoothly as possible. These are some of the roles a great 3PL partner can play during a product recall:
- Leveraging expertise and resources
- Strategic recall planning
- Efficient reverse logistics
- Communication and stakeholder management
Now, let’s discuss them one by one.
Leveraging Expertise and Resources
A great 3PL partner brings skills, experience, and adaptive resources to help with a recall- making them an invaluable asset in a recall scenario. They possess the industry knowledge to create effective strategies to manage the recall process and prevent the spread of any affected products.
They can handle complex supply chains, with customers requiring tailored responses- including cold storage, transport services, or fulfillment. Therefore, they will provide a clear understanding of the compliance requirements, potential regulatory changes, and the impact of the recall on logistics operations.
Strategic Recall Planning
Effective communication and cooperation between the business and the 3PL Partners are essential for successful planning. This includes understanding the logistics operations of the affected products and organizing the end-to-end strategy, which will vary depending on the nature of the recall.
A great 3PL partner will critically assist in developing and executing this strategy for the business to minimize the risk and keep its operations running. This can include a review of the supply chain, supplier management programs, and integrated business systems for enhanced visibility. They will further take this opportunity to analyze the causes of the recall, learn from the mishap, and ensure that improvements are implemented.
Efficient Reverse Logistics
Reverse logistics is an integral component of the recall process, which focuses on retrieving, transporting, and disposing of the affected products as quickly and profitably as possible.
“In reverse logistics, the products will undergo either of these following processes:
- Remanufacturing: The product is rebuilt using new, reused, or repaired parts.
- Refurbishment: Products are resold after the original product is repaired and after it undergoes proper quality checks.
- Servicing: In the case of servicing, any specific damaged part is fixed or replaced and returned to the original customer.
- Recycling and waste management: Products are returned to the manufacturer, and those that can’t be fixed are recycled into parts of another product. This reduces the waste generated by the company and promotes the concept of Green Logistics (Rouse, 2016).”- Anuj Sharma, Ninaad C. Kikkeri, Ilaanshi Varma.
An effective 3PL partner should have a comprehensive cross-functional team with specific experience and expertise in the reverse logistics process. They will also have the necessary network of transport options to expedite the process and ensure all affected products are retrieved and disposed of responsibly. This dedicated skill set and expertise in reverse logistics can also assist businesses in improving long-term sustainability goals and cost-effectiveness.
Communication and Stakeholder Management
During a recall, communicating timely and effectively with different stakeholders will help organizations mitigate risks and minimize damage to their reputation and finances.
This includes clear communication with customers, suppliers, distributors, regulatory agencies, and other third parties who could be impacted.
A great 3PL partner understands the benefits of effective communication with stakeholders, saving time and money and reducing brand damage in the long run. They have streamlined reporting systems and provide data integration into an organization’s recall management strategy. Furthermore, a 3PL partner can also help reduce regulatory impact by liaising with relevant authorities before, during, and after a recall- ensuring all requirements are met.
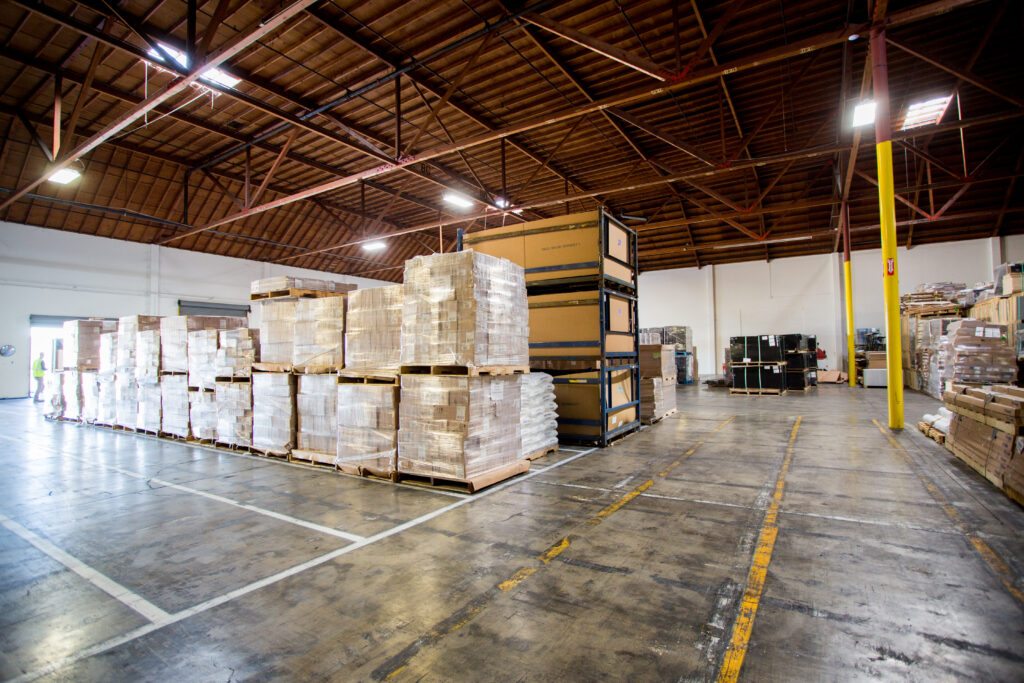
Benefits of Partnering with a Great 3PL
When facing a product recall, partnering with an excellent third-party logistics (3PL) provider can significantly mitigate any risks. The global logistics market is constantly evolving in today’s competitive business world- making it difficult for businesses to run without the help of a reliable 3PL partner.
They can provide transport services, but 3PLs can help businesses improve their supply chains, fulfillment strategies, and customer experiences. “The Annual Third-Party Logistics Study continues to show that shippers and third-party logistics providers generally report benefits from their relationships, even as supply chains have been under stress both domestically and abroad.”- Third-Party Logistics Study
There are numerous benefits of partnerships with 3PL partners. Here we’ll discuss a few of them:
- Improved Supply Chain Management
- Reduce Costs
- Expertise and Experience
- Flexibility
- Additional Capacity
- Improved Customer Service
- Regulatory Compliance and Reporting
- Brand Protection and Reputational Safeguarding
- Risk Mitigation and Preparedness
Improved Supply Chain Management
Partnering with a great 3PL provider can streamline your supply chain management by optimizing distribution, inventory, and order fulfillment. With their expertise, businesses can effectively manage their supply chain during a recall. A great 3PL partner, like FDR Warehouse, can provide a wide range of warehousing solutions to meet the unique needs of small businesses to large corporations.
We offer long and short-term storage, cross-docking, dispatching, local transportation, and value-added services like palletizing, barcoding, labeling, drainage, and shrink wrapping. This can significantly improve supply chain management during a product recall.
Reduce Costs
Outsourcing logistics to a 3PL partner can help businesses reduce transportation and labor costs. Instead of investing in expensive warehouses and vehicles, companies can work with a 3PL partner with the infrastructure to handle their product recall needs. This can help reduce the overall cost of a product recall.
3PL providers can also offer faster and more efficient shipping options to help save on shipping costs for businesses looking to manage their expenses during a recall. Additionally, partnering with a 3PL provider can provide access to technology investments that businesses may not have access to otherwise.
Expertise and Experience
A great 3PL partner can provide businesses access to the logistics expertise that may be missing in-house. They can offer guidance and help throughout a product recall process. Experienced 3PL partners can assess the real-time recall situation, perform quality control checks, repackage products, and navigate regulatory requirements. They can advise businesses on the most cost-efficient and effective supply chain solutions, which can improve their logistic operations.
Flexibility
Businesses need more flexibility than ever before during a product recall. A great 3PL provider can help companies quickly and efficiently adapt to changing conditions- such as those produced by a product recall.
3PL providers can be integrated seamlessly into a company’s existing supply chain- providing the extra capacity and flexibility to handle the recall situation. Additionally, they can customize their services to meet the unique requirements of each business.
Additional Capacity
Partnering with a 3PL provider can offer businesses additional capacity and flexibility for their recall process. With access to a 3PL network of warehouses, transportation providers, and supply chain professionals, companies can expand their power during the recall process.
3PLs can help businesses handle higher order volumes or sudden surges of demand- ensuring that customers receive their orders on time, strengthening the relationship between the company and the customer.
Improved Customer Service
Customers are the lifeblood of any business, and a product recall can put a business’s relationship with its customers at risk. Partnering with a great 3PL provider can help companies to improve their customer service by offering faster, more efficient shipping and handling of returns.
3PL partners can also offer additional services- such as package labeling, item tracking, and return processing, which can help create a better customer experience.
By strengthening customer relationships, businesses can increase customer loyalty, grow their brand and create more business opportunities.
Regulatory Compliance and Reporting
Compliance with regulations is a crucial aspect when it comes to product recall. Outsourcing this challenging task to a 3PL partner can give businesses the time to focus on product recall and ensure they follow the set regulations.
A 3PL partner ensures local, national, and international regulatory requirements compliance. It helps businesses with reporting obligations and coordinates communication with respective government agencies.
Brand Protection and Reputational Safeguarding
Protecting a brand image is always a priority for businesses. A trusted 3PL partner can help protect their brand image and maintain customer trust in a product recall.
A 3PL partner effectively handles all the logistics required to execute a recall. It also communicates with the respective government agency and the public on behalf of businesses. Doing so helps to reassure customers that the companies are taking all necessary steps to ensure customer safety and satisfaction.
Risk Mitigation and Preparedness
A 3PL partner can help businesses minimize risks by ensuring proper inventory tracking, secured storage, and timely execution of recall activities. This preparation helps determine the logistics in advance, enabling businesses to mitigate risks associated with recalling a product. A good 3PL partner allows companies to develop an effective recall strategy and plan and review their existing ones.
Tasks Performed by a Great 3PL Partner during a Product Recall
Recalls are a business nightmare and can cause mayhem if not handled quickly and efficiently. Product recalls can happen anytime- and businesses must have an effective recall strategy to mitigate the risks. A great 3PL partner can assist a business during a product recall.
Here are some of the tasks a great 3PL partner can perform during a product recall:
- Recall Planning and Strategy Development
- Product Traceability and Documentation
- Reverse Logistics Management
- Inspection and Quality Control
- Rework and Repackaging
- Provide Crisis Management
- Protecting a Business from Liability
- Maintaining Communication and Transparency
- Customer Service and Support
- Data and Analytics
- Forecasting and Strategy for Future Recalls
- Continuous Improvement
Let’s discuss them all one by one now.
Recall Planning and Strategy Development
Planning and strategy development are critical to mitigating the risks associated with product recalls. 3PL partners can collaborate with businesses to develop comprehensive and effective recall plans and strategies.
A strong partnership can ensure that the recall plan factors in the partner’s experience, capabilities, and resources can avoid additional costs and delays and give the customer potential savings.
Product Traceability and Documentation
Product traceability is a critical component of any recall. A great 3PL partner can help you track your products throughout the supply chain- ensuring that you know exactly where each product has been and what processes it has undergone. They can also help you document affected products and manage the flow of information to customers and suppliers.
Reverse Logistics Management
The retrieval, transportation, and disposal of affected products is a complex process that requires expertise and attention to detail. Your 3PL partner can handle all aspects of this process- from coordinating with suppliers to arranging transportation to managing disposal.
By having a partner specializing in reverse logistics, you can minimize the disruption to your business and ensure that the recall is handled promptly and efficiently.
Inspection and Quality Control
Maintaining a high level of quality control during a product recall is critical to ensure that the recall is effective and that no affected products slip through the cracks. Your 3PL partnership can support the inspection and quality control processes- helping to identify affected products, test them to ensure they meet quality standards, and manage the reworking or repackaging products as necessary.
Rework and Repackaging
In some cases, affected products may be able to be reworked or repackaged rather than disposed of. Your 3PL partner can help you determine whether this is feasible and can support the reworking and repackaging process as needed. This can help minimize the impact of the recall on your business and customers.
Provide Crisis Management
Businesses should have a crisis management team to handle the situation during a product recall. Your 3PL partner can provide crisis management support- helping you navigate the challenges associated with a recall and ensuring that your business can manage the crisis effectively.
Protecting a Business from Liability
A good 3PL partner will know the legal requirements associated with product recall and ensure strict compliance. They are responsible for disposal and can also provide proper documentation for insurance claims, which may prove valuable in future legal proceedings.
Maintaining Communication and Transparency
Effective communication is integral to managing business relationships during a product recall. A 3PL partner that provides transparency and maintains open communication channels will significantly aid the business in the recall management process.
Customer Service and Support
It’s essential to maintain open lines of communication with customers and suppliers during a recall. Your 3PL partner can help you manage customer inquiries, provide status updates, and ensure all stakeholders are informed and engaged throughout the process.
Data and Analytics
Data and analytics are also essential factors during product recalls. A 3PL partner can provide data on the status and movement of products during a recall- including inventory, orders, deliveries, and return shipments.
This data can be used to identify problems earlier, prevent further complications, and manage financial risks. It’ll also help to understand the impact of the product recall on the company overall and provide insights to make informed business decisions.
Forecasting and Strategy for Future Recalls
Once a product recall has occurred, a strategic 3PL partner can help the company to create protocols for future recalls- minimizing the risks of such occurrences. A professional 3PL partner can leverage data analytics to identify potential product defects that may lead to future recalls.
Continuous Improvement
A great 3PL partner can help you identify areas for improvement in your recall processes and procedures. By conducting post-recall assessments and working with you to develop new strategies and techniques, they can help you prevent future recalls- ensuring the ongoing success of your business.
FDR Warehouse in Stockton, California- A Reliable 3PL Partner for All-Size Businesses
Finding the proper warehousing and logistics partner is crucial for businesses of all sizes, especially when facing a product recall.
FDR Warehouse in Stockton, CA, is a trusted third-party logistics partner that helps businesses manage their supply chain; especially during crises like product recalls.
Conveniently located close to the Union Pacific and BNSF railways, I-5, Highway 99, Highway 4, and Port of Oakland and Port of Stockton, FDR Warehouse makes transportation, distribution, and fulfillment easier and faster- saving businesses time, money, and resources.
Third-Party Logistics Partner Offering Global Logistics Solutions
FDR Warehouse offers various logistics services that help businesses grow, scale, and outsource their supply chain needs. It eliminates the need for businesses to manage their inventory, shipping, and fulfillment in-house, which can be costly and time-consuming- and allows them to focus on their core competencies while leaving the rest to FDR Warehouse.
Flexible and Scalable Solutions to Meet Unique Business Needs
FDR Warehouse offers long and short-term freight storage, cross-docking, dispatching, local transportation, and value-added services- including palletizing, barcoding, labeling, drainage, and shrink-wrapping. The services are flexible and scalable to meet the unique needs of each business, whether it’s a small or large order, short-term or long-term storage, or any other requirement.
24/7 Customer Support
FDR Warehouse’s dedicated customer support team is available 24/7 to help customers with any questions, concerns, or issues. The team is knowledgeable, responsive, and helpful- ensuring customers have the best experience possible.
Cost-Effective Services
The cost of FDR Warehouse’s services depends on factors such as the type of storage, the number of pallets, and the storage solutions needed. However, the services are always cost-effective- helping businesses save on warehousing costs, transportation costs, and supply chain touchpoints.
A Safe and Secure Storage Facility
FDR Warehouse understands the importance of safety, especially during product recalls. That’s why it offers a safe and secure storage facility, with 24/7 surveillance and regular checks for pests and bug infestations- ensuring the products are in good condition and ready for distribution.
The Best 3PL Company in Stockton, California
FDR Warehouse is known for being Stockton’s best warehousing and logistics company- offering exceptional services, unmatched customer support, and cost-effective solutions.
Its focus on scalability, flexibility, and efficiency has earned the company a reputation for being a trustworthy and reliable partner that helps businesses grow, manage crises, and succeed.
Final Words
Product recalls can be stressful and costly for businesses. Still, companies can easily avoid mayhem and manage their supply chain needs with a great 3PL partner like FDR Warehouse in Stockton, CA.
FDR Warehouse offers flexible, scalable, and cost-effective logistics solutions, 24/7 customer support, and a safe and secure storage facility- making it a reliable partner for businesses of all sizes. Request a quote at (209) 780-5042 or schedule a time on our calendar now.