Can Your Warehouse Impact Your Holiday Season Sales? Yes!
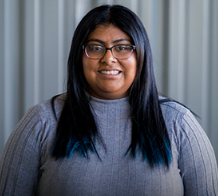
Melissa Cruz
Sales Coordinator
The holiday season is an exciting time for businesses that anticipate a surge in sales and heightened demand for their products. However, although it is a great time for businesses to generate revenue, it can also be fraught with challenges. Indeed, one of the most crucial aspects of a successful holiday season is efficient warehouse management and logistics.
In this article, we will explore the role of warehouses in holiday sales, common warehouse issues during the holidays, the benefits of warehouse technology and automation, and the importance of planning ahead and potentially switching warehouses.
We will also discuss FDR Warehouse in Stockton, CA, and what it can offer to businesses looking for storage solutions. So, let’s start it!
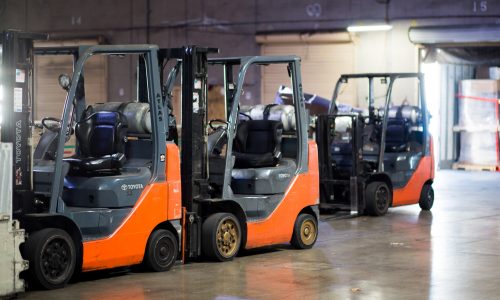
The Role of Warehouses in Holiday Sales
A warehouse serves as the physical space where a retailer or distributor stores their inventory before it is shipped out to retailers, wholesalers, or directly to customers.
There is often a substantial increase in the number of orders placed during the holiday season- and it is not uncommon for inventory levels to fluctuate. Hence, warehouses play an integral role in holiday sales revenue.
That said, warehouse management and logistics during the holiday season can be challenging. Managers must ensure they have enough inventory to meet the anticipated demand, but they must also be careful not to overstock, which can tie up capital and create excess inventory down the line. The emphasis should be on maintaining optimal inventory levels to meet customer demand without causing delays or stockouts.
Common Warehouse Issues During the Holidays
While warehouses can work tirelessly to maintain optimum inventory levels, they can still fall prey to issues that threaten to derail their holiday sales. Below are some common warehouse issues that can occur during the holiday season.
Overstocking
Overstocking can occur due to poor sales forecasting, where a warehouse has an excess amount of stock. Overstocking can result in tying up capital that can be invested elsewhere- and in some instances, it can lead to the accumulation of obsolete inventory if sales do not go as planned.
Understocking
A lack of inventory can occur when sales forecasting is inaccurate, which can result in stockout situations, delayed shipments, and loss of revenue.
Delayed Shipments
Shipping delays can occur due to inclement weather, freight carrier capacity limitations, and a shortage of warehouse staff. These delays can impact customer satisfaction and revenue.
Inventory Inaccuracies
Human error can result in inaccurate inventory counts, which can lead to delays in order delivery or stockout situations- ultimately leading to a loss of revenue.
Warehouse Technology and Automation
Warehouse technology and automation can help businesses overcome some of the common challenges associated with managing a warehouse during the holiday season.
A 3PL warehouse, like FDR Warehouse, with advanced technology and tools offers businesses some of the following solutions to overcome their challenges.
- Inventory management software can help businesses keep track of their inventory levels and ensure they have enough products to meet demand.
- Automated picking systems can help streamline the order fulfillment process- reducing the time it takes to fulfill orders and increasing accuracy.
- These technologies can also help businesses reduce labor costs and improve efficiency- allowing them to process more orders in less time.
- Warehouse automation can also improve worker safety by reducing the amount of heavy lifting and other physically demanding tasks.
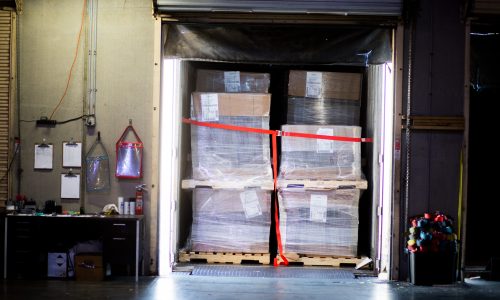
The Importance of Planning
Planning ahead is critical for all businesses during the holiday season. Business owners must plan for increased demand during the busiest shopping season of the year, prepare their warehouses for handling the influx of orders, and ensure that their staffing levels are appropriate to meet consumer demand. It is absolutely necessary to secure a warehousing partner in either Q1 or Q2 of the year. Your plan and warehousing partner needs to be set in place no later than July in order to maximize potential on the upcoming holiday season.
One essential planning tool is forecasting software, like Stocktrim, which can help businesses track sales patterns, predict demand, and make decisions based on data. Additionally, businesses must maintain good communication with their warehouse provider to ensure that their inventory is adequately managed.
FDR Warehouse in Stockton, CA- A Complete 3PL Warehouse Solution to Manage Increased Holiday Sales
FDR Warehouse is a warehouse and logistics solutions provider in Stockton, California that can help businesses handle their warehouse issues during the holiday season. With two facilities located in Stockton, we offer flexible and scalable solutions to meet the unique business needs of our clients.
We provide both long and short-term freight storage, cross-docking, dispatching, local transportation, and value-added services- including palletizing, barcoding, labeling, dredging, and shrink wrapping.
FDR Warehouse understands that managing your inventory and supply chain during the holiday season can be challenging, which is why we offer round-the-clock, 24/7 customer service.
Our prime location provides convenient access to the Union Pacific and BNSF railways, I-5, Highway 99, Highway 4, and the Port of Oakland and Port of Stockton.
To request a quote, businesses can contact us at (209) 780-5042 or schedule a time on our calendar.